5 questions on woodworking – and the perfect drive
The special features of sawing, drilling and more
KEB Automation stands for innovative drive and automation solutions for woodworking machines. Robert Otto is a sales engineer at KEB and knows the challenges of the industry inside out. In this interview, he explains what makes system solutions in woodworking so special and why a design that has not been thought through properly can, in the worst case, lead to a fire.
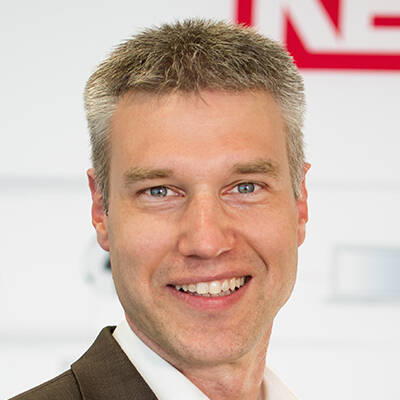
What distinguishes the drive design for woodworking machines from other applications?
Otto: For every single machine or plant, we always insist on finding individual automation and drive solutions. One special feature of woodworking is that it covers so many different facets. Whether it's edge processing or machining solid wood, for example, this has an impact on the requirements for the drive. This also means that we have to be particularly flexible in our design in order to be able to map the various machining processes and materials on the drive side.
With a material like wood, imprecise work is immediately noticeable. That's why precision is so important here, which we take into account when designing the KEB solution to avoid vibrations or other inaccuracies. We also make sure that the components are robust and durable even under harsh environmental conditions with chips and dust. In addition, we may also need to achieve high torques at low speeds, which is required when machining solid wood, for example. To date, we have already commissioned countless systems and draw on our experience in discussions with our customers to find the best drive solution together.
High-speed spindles are a special area of application in woodworking. What should users look for in drive components for spindles?
When we talk about drives, we at KEB have the entire system solution in mind: from IIoT and the appropriate control to motors and drives. Our COMBIVERT F6 and S6 drives have been established for a long time and have the advantage that they can be used to control a wide variety of motor variants, including high-speed spindle motors. Encoderless positioning and speed stability up to 120,000 rpm are possible without any problems. Based on the precise motor data, the behaviour of the drive controller and motor can be calculated at critical operating points. Another practical feature for operating high-speed spindles is that our drives have a multi-encoder interface but can also be controlled or operated without an encoder with the KEB motor model and are designed for the safe field weakening range.
Safety plays an important role in woodworking. How does KEB meet the high requirements in this regard?
In order to design the processes and movements of woodworking machines, where saw blades rotate at high speeds and different tools with different maximum speeds are monitored, in a flexible and safe manner, it is essential to map functional safety in its entirety. At KEB, we ensure the required level of safety on several levels: through safety controllers, various safe variants of fieldbus communication, (geared) motors and brakes – and, of course, through safety functions that are directly integrated into our COMBIVERT drive controllers. This starts with secure communication with Safety over Ethercat or via PROFIsafe. With SLS (Safely-Limited Speed), KEB drives safely monitor the speed of the woodworking machine's drive. If the set speed limit is exceeded, an error response is triggered and tools are protected against overspeed. With SDLC (Safe Door-Lock Control), we offer an application-specific feature that ensures the machine cover only opens when the motor is safely at a standstill – this is relevant when changing tools, for example. These are just a few examples of the extensive speed- or position-dependent safety functions available, both with and without a safe encoder.
What precautions can be taken to ensure the best possible fire protection?
When working with wood, fire protection is an issue that should not be underestimated. In the worst case, leakage currents of just 300 mA are enough to start a fire. 300 mA residual current circuit breakers are therefore essential, especially in woodworking machines. With COMBILINE E6, KEB has a filter series in its portfolio that contributes to greater fire protection: Various solutions with low residual current filter solutions in connection with the inverters enable the operation of residual current circuit breakers. The E6 filters are available as separate units in the form of auxiliary or sub-mounted filters, depending on the device series and size, but also as variants integrated into the device.
For which specific applications in the field of woodworking does KEB offer solutions?
Woodworking has a wide range of applications, and it is important to find the perfect solution for each individual application. One major area is certainly CNC technology, for which we offer a system consisting of hardware and software components. A scalable CNC control system with ready-made modules makes commissioning and visualisation particularly easy. With IPCs, HMIs and our drive controllers, we are also at home in edge processing. Sawing, drilling, milling, grinding: all these are part of surface technology, for which we implement cost-effective complete packages for automation and drive technology. We use (gear) motors with up to 1.3 MW in solid wood, among other areas, and we implement transport and handling tasks through the encoderless positioning of synchronous motors or the smart software functionalities in the drives.
