Brakes in machine engineering: the latest trends
Interview with Sales Manager Kevin Zysk
How are requirements in mechanical engineering changing and what impact is this having on the brakes used? And what is advisable to ensure the availability of brakes even in times of strained supply chains? In this interview, Kevin Zysk, Head of Sales for Brakes and Clutches at KEB Automation, talks about the need for flexibility in the brake sector and alternatives to rare earths.
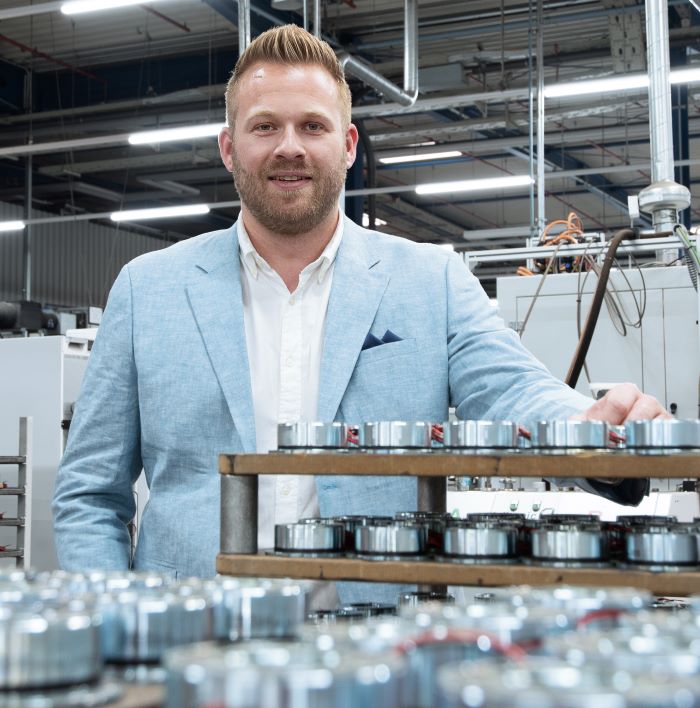
KEB brakes are used in a wide variety of applications. In your experience, which brakes are currently the most commonly used?
Zysk: That always depends on the application. Spring-applied brakes, our COMBISTOP series, are mainly used in cranes, lifts and industrial trucks. Permanent magnet brakes, on the other hand, are increasingly used in servo motors. I am thinking here, for example, of the COMBIPERM products, which are optimised and adapted for use in servo motors. Of course, we also have service brakes in our portfolio, such as the COMBINORM B with friction lining or as a toothed version. These ensure precise positioning and reliable holding and are often used in access systems or woodworking machines.
Which brake properties are particularly important to users?
Thanks to our wide range of products, we can offer the right brake with specific properties for almost any application. Even though individual requirements always have different priorities, compact brake dimensions are very much in demand. With a view to optimum planning and delivery times, brakes that are completely independent of materials such as rare earths are particularly interesting in light of current export regulations. These are components of permanent magnets, among other things. We therefore offer an alternative to permanent magnet brakes with our new patented friction pad system, which does not require permanent magnets and offers similar performance in the same installation space. It also reduces fine dust emissions to almost zero. The high-performance COMBISTOP S1 holding brake, for example, features this friction lining system and will certainly remain an exciting option in the future when it comes to maximum material independence.
To what extent have customer requirements and wishes regarding brakes changed in recent years?
There are factors, such as the situation with rare earths that we just mentioned, that require a response and therefore inevitably change the requirements for brakes. In times of complex supply chains, it is crucial that the availability of brakes can be planned as far in advance as possible. In addition, customers predominantly rely on holding brakes with an emergency stop function instead of service brakes. However, we are also seeing that individuality is becoming increasingly important – and that is precisely where our strength lies at KEB. Where standard solutions are not sufficient, we develop and manufacture customised brakes in close consultation with our customers. Our motto is: nothing is impossible. If, for example, installation space is limited but high torque is required, we can usually implement this without any problems thanks to our high level of vertical integration.
What impact do changing requirements have on the production process?
A high degree of flexibility is required, from development and production to sales. The creation of installation proposals as 3D models, based on magnetic flux calculations and simulations, enables us to map a realistic implementation of the customer's requirements in the shortest possible time. Based on the installation proposal, we work with the customer to develop the most economical and technically suitable solution step by step. In production itself, high-precision, partially automated turning and milling machines, among other things, ensure that the individual brake solutions are implemented. High quality and cost-effectiveness are paramount here.
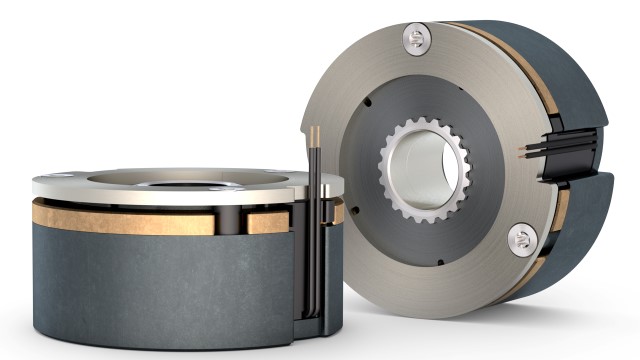
How do you see KEB positioned for the future and the competition?
Brakes and clutches laid the foundation for KEB in 1972 and will continue to be an important part of our overall portfolio. With innovative new products such as the new patented friction lining system, we ensure that our range of brakes keeps pace with the times. Our brakes are ‘Made in Germany’. I see this not only as a promise of quality, but also as a guarantee of independence, flexibility and speed in responding to changing market situations. We manufacture our brakes in-house, which allows us to influence the end product at several points in the development process in order to meet customer requirements. We have been present in areas such as medical technology, robotics, AGVs and general servo motors for a long time. And we are constantly opening up new and exciting application areas and market potential, such as construction machinery.
What new brake models can KEB customers look forward to in the near future?
New models are based on existing, reliable technology, but feature new and innovative technical solutions. When customers specify requirements such as intermediate sizes, hollow shaft applications, toothed variants, bistable brakes for energy saving or high maximum emergency stop speeds, we are usually already familiar with these from past experience. This is also reflected in our production programme: an estimated 80 percent of our production consists of customer-specific variants that are not listed in our catalogue, and only 20 percent are standard products. A real innovation is the new patented friction lining system, which we are now increasingly offering our customers in the field of servo motors, AGVs and robotics.