Maximum safety in woodworking
3 Questions on bonnet locking, fire protection and more
Material, surface and solid wood processing, transport and handling: KEB Automation offers the right drive solutions for the core areas of woodworking machines. And as different as the requirements for the drive controllers are, one topic is always in focus: the creation of the highest possible level of safety. Robert Otto, Application Engineer Automation and Drives at KEB, explains how plant and machine builders can achieve exactly this.
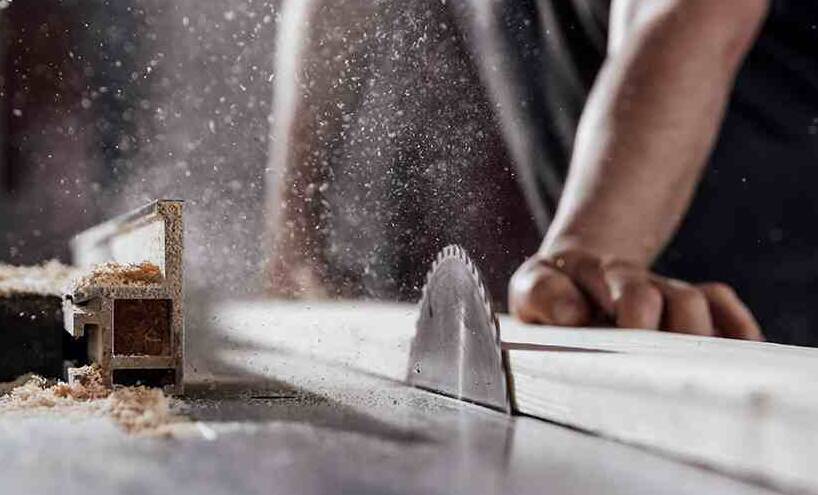
What is the fundamental significance of functional safety in the woodworking sector and how does KEB implement it?
Robert Otto: Functional safety is intended to keep the risks posed by technical equipment to people and the environment as low as possible. Let's think of processing machines or machine tools, for example. These can endanger machine operators through tools that rotate at too high of a speed. To prevent this from happening in the first place, we at KEB rely on drive solutions that ensure the safety functions with or without encoder. To avoid dangerous operating conditions, safety functions monitor the speeds, directions of rotation or axis positions. Because safety functions are already integrated in our drive controllers and interact optimally with our safety controllers, users can implement functional safety particularly cost-effectively.
Among the safety features integrated in the COMBIVERT drives are functions that KEB has developed itself. What are these features?
In the PRO variant, the COMBIVERT F6 Drive Controllers and S6 Servo Drives have Safe Door-Lock Control (SDLC) with Performance Level d (PL d). We developed this function at KEB and it can be used to lock the bonnet of the machine. With SDLC, the bonnet can then only be opened when the motor is at a safe standstill, for example, in order to be able to change tools or to allow the machine to be cleaned. In addition, of course, we offer further speed- and position-dependent safety functions such as Safe Speed Monitoring (SSM) or Safely Limited Speed (SLS), also in combination with Safe Direction (SDI), whereby the drive safely monitors the speed. If the set speed limit is exceeded, an error reaction takes place and tools are ultimately protected from overspeed by SLS. And of course we at KEB also rely on safe communication – as an established solution with Safety over EtherCAT (FSoE) or also with PROFIsafe, which is integrated in the APPLICATION device variant of our drives.
Fire protection is particularly relevant when working with a raw material such as wood. What does KEB do to prevent fires in woodworking machines?
In woodworking, fires can start faster than one might think. Even leakage currents of 300 mA can trigger a fire in the worst case. That is why 300 mA residual current circuit breakers are required in the machines. With this in mind, we have developed the COMBILINE E6 filter series, which is implemented in the latest generation of inverters and which feeds the leakage currents in the inverter-cable-motor-network back into its own system. The filters are available as sub-, auxiliary- or collector filters and contribute to reducing leakage currents to a minimum and to lowering the risk of fire.
See our solutions for woodworking machines live
We are looking forward to your visit.
