Servo pump control: Our solution for hydraulic systems
Reduced cycle time, pump protection and efficient commissioning
For hydraulic systems with highly dynamic control technology requirements, the servo pump is the ideal solution for plant and machine manufacturers. KEB offers you an efficient and convenient software-based servo pump control function – perfect for plastics processing, hydraulic and press brakes, as well as applications in the field of lift technology.
Benefit from the KEB servo pump solution in several ways: you reduce the cycle time, lower energy consumption and noise emissions, extend the service life and thus save money. Get an overview of your options with KEB on this page and contact us for your customised servo pump solution.
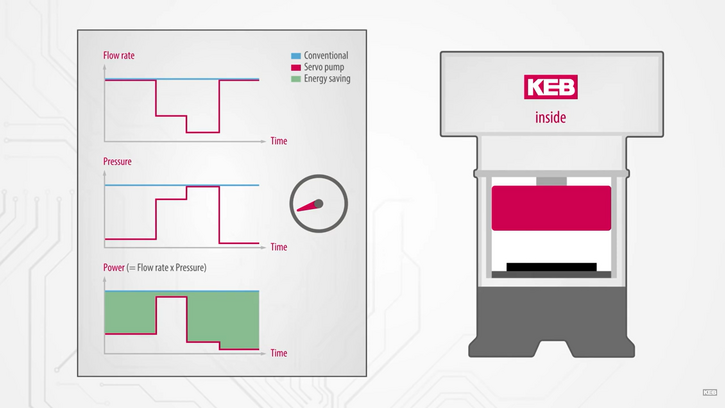
What are the benefits of servo pump control?
In times of increasing costs, one aspect is particularly important in plant and machine engineering: efficiency. Against this background, KEB's servo pump solution enables shorter cycle times and smaller pump sizes thanks to the system-related possibilities offered by the multi-hydraulic selector.
The energy-efficient operation of a system such as an injection moulding machine is not only ecologically sensible, but is also more important than ever for cost reasons. This is because conventional hydraulic systems are operated directly from the electrical network. Unregulated operation results in constant pressure and flow, which leads to high energy consumption. KEB's servo pump control in combination with the right servo motors remedies this and reduces energy consumption by up to 70 percent.
And there are even more benefits for you:
- Reduced cycle time and pump size
- Lower energy consumption, reduce costs
- Up to 20 dB (A) quieter: Less noise emissions because motor only runs when needed
- Fewer components in the system
- Less maintenance required
- Longer service life of your machine due to lower heat generation
- More productivity thanks to increased machine availability

Tim Aufderheide
Application Automation and Drives
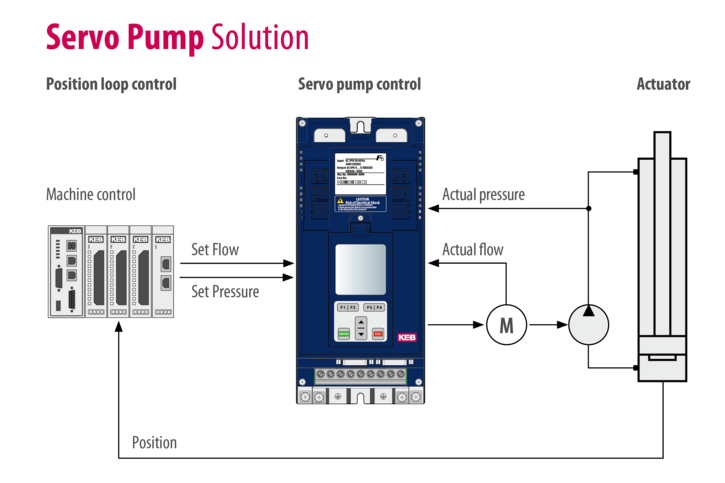
How does our servo pump solution work?
A servo pump system usually consists of a gear pump, servo motor and frequency inverter. The KEB solution for servo pump control is located in exactly this inverter: The integrated software in our tried-and-tested COMIVERT F6 and S6 drive controllers has an algorithm with which the flow and pressure of the servo pump can be regulated. Adaptability to the machine requirements is a major advantage for injection moulding machines, for example, as cycle times are particularly relevant here. Pump protection is realised through corresponding software features and parameters.
KEB Automation provides you with system solutions comprising controller, inverter and motor from a single source for your application. One example: The interaction of KEB drive controllers with servo pump control and our servo motors from the DL4 series achieves particularly high dynamics. A powerful combination that also saves energy. Commissioning of the system is simplified by a wizard for guided parameterisation of the application and the auto-tuning function (calibration to the hydraulic circuit). The adjustment of the pump speed in the partial load range and outside the operating cycle, in combination with volume flow or pressure control directly via the pump system, ensures economical implementation of your hydraulic machines.
Benefit from performance, pump protection and high-precision control without compromise. Our experts will be happy to advise you.