Apprentice project: Three weeks AC/DC
KEB, Lenze and Weidmüller work together for greater energy efficiency
With a share of 38 percent, industry is one of the largest energy consumers in Germany. There is a lot of potential for reducing energy consumption and conserving resources. One possibility: converting factories from alternating current (AC) to direct current (DC). Five trainees from KEB Automation, Lenze and Weidmüller implemented the "DC Industry" concept in a joint project at the end of February.
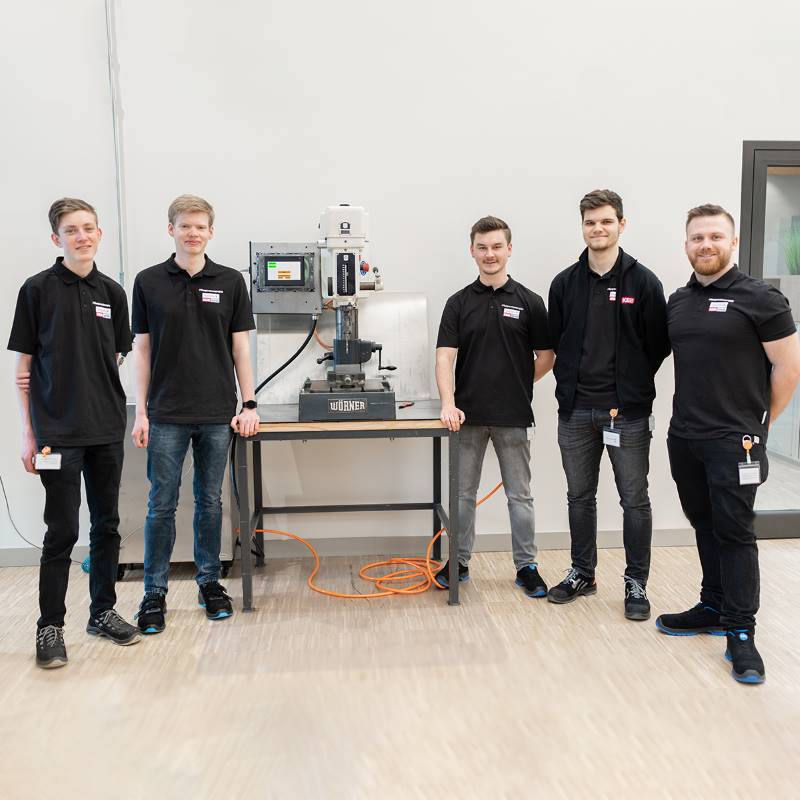
The task of Marvin Günter (KEB), Jannis Brand and Felix Heiland (Weidmüller) as well as Moritz Drinkuth and Hannes Schneider (Lenze) was clear: within three weeks, the trainees were to convert a floor-standing drilling machine to DC technology and thus gain initial experience with the future topic of DC industry. Now they presented their results. "It is so motivating to be able to take part in the future-oriented "DC infrastructure" project at the Weidmüller Academy in Detmold and to see how enthusiastically the trainees implemented the floor-standing drilling machine project with all its ups and downs," said a delighted Thomas Möllerfriedrich, the project coordinator from Weidmüller. The trainees entered completely new territory with the project. Not only did they have to find each other as a team, but they also had to be introduced to the new topic of DC networks.
After the status quo analysis, it was time for the conversion planning and procurement, then for the actual conversion and commissioning of the system. "In the three weeks, we learned how complex projects can become that seemed quite simple to us at the beginning," summarises Marvin Günter, apprentice electronics technician for devices and systems at KEB.
The team built a mobile energy feeder that maps a DC network and integrated a human-machine interface (HMI) to control and visualise the system, which in future can be operated by "touch" and also provides energy data. A new motor with frequency converter for electrical speed adjustment is used. With the successful completion of the project, the five apprentices were able to show that the concept provides the desired improvements. Torben Müller, a trainer at Weidmüller, sees that such joint projects are gaining in importance, especially in times of a shortage of skilled workers: "The trainee project is an incredible opportunity for the trainees and the region to help shape the future development of energy supply. It also shows how important it is for apprenticeship companies to work together to ensure the best possible development and training for apprentices."
The key to a sustainable factory of the future
The apprentice project grew out of the DC-Industry2 research project, in which 39 partners from industry and research worked together to develop the basics for a direct current infrastructure in industry. Entire production halls can be powered by direct current (DC) from renewable energies and the benefits are considerable. Some examples:
- Renewable energies can be integrated more easily. The factory thus becomes an energy producer and consumer at the same time.
- Fewer conversions from AC to DC and vice versa reduce losses and energy consumption.
- The feed-in power from the central supply grid is lower.
- DC systems have higher availability because they continue to run from their own storage if the utility grid fails.
- The converters required for energy-efficient drives are smaller (up to 25 percent less volume). Many components needed for alternating current can be eliminated altogether.
Find out how the DC-Industrie2 research project is already making modern and efficient industrial production possible in TechTuesday on the topic of "Saving in the DC network":
