How safety gets into robots
Brakes from KEB Automation in robotics
Industrial robots are taking on more and more tasks in production. They assemble, transport - and ensure greater efficiency. With this level of automation, brakes that guarantee precision, speed and safety are particularly important. But how can they precisely meet these requirements? Which brake is best suited for use in industrial robots, cobots and co?
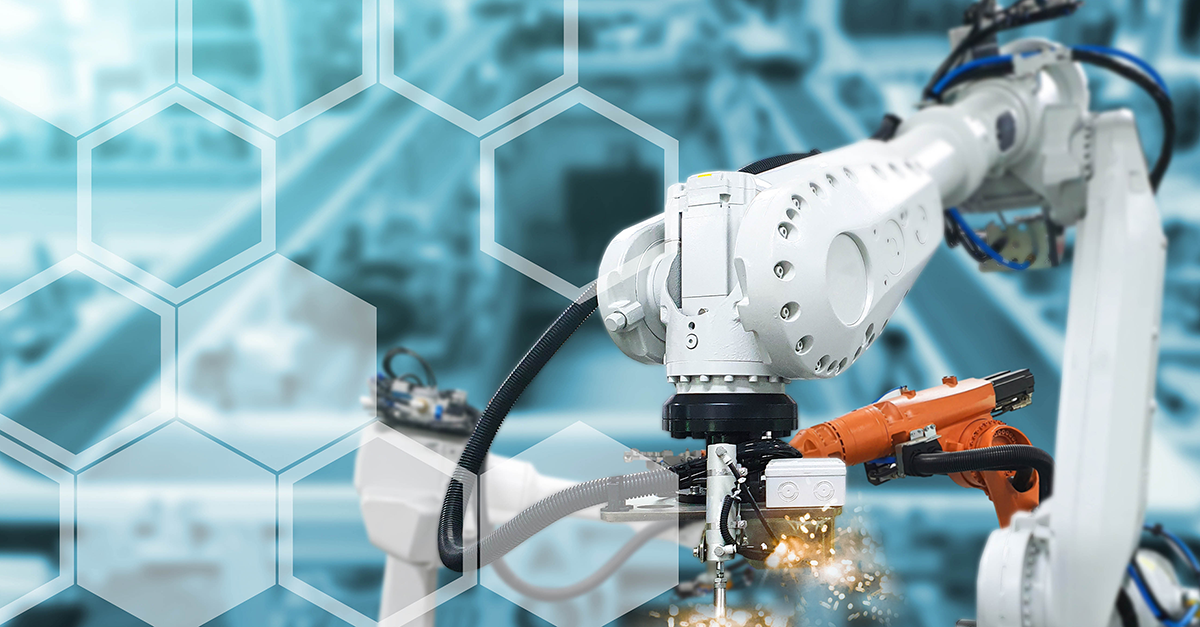
As a result of growing automation, industrial robots are increasingly being used for repetitive work steps. They save costs and reduce the workload of the employees in the company. And robotics can also help with more individual work processes: Cobots, for example, are used to improve working conditions and facilitate processes – while maintaining the quality of the products. Regardless of whether robots are used in industry, medicine, warehouse logistics or in the agricultural sector, the following applies: wherever masses must be braked and held securely in one position, brakes are required that can reliably perform these tasks.
“Fast movements with large masses, such as a car body, are commonplace in robotics. This generates a high mass inertia and thus a high torque. The brake now has the task of holding the robot arm in position and braking the movement safely in an emergency. For this case, there is a safety brake that is actuated in a de-energised state,” says Kevin Zysk, Head of Sales Brakes and Clutches at KEB.
The specific requirements for the brake differ depending on the application. While compact brakes with a high power density are required in medical technology to meet the high safety standards, brakes that are easy to install are particularly relevant in industry. Still other areas of application require a particularly high positioning accuracy, so that a backlash-free brake is necessary.
“With the COMBISTOP spring-applied brake and the COMBIPERM permanent magnet brake, KEB offers its customers the right brake solution for different robotics applications. In consultation with the customer, we determine which brake best fulfils the specific requirements and which changes we make to the standard to deliver the best possible solution”, says Zysk. The individual advantages of the spring-applied or permanent magnet brakes become apparent during the selection process:
The COMBISTOP has a torque of up to 4,000 Nm and is constantly and safely closed once the wear limit has been reached. In addition, the spring-applied brake can be equipped with further accessories such as a microswitch for monitoring the wear and condition of the brake or a hand release lever for manual brake release. The COMBIPERM permanent magnet brake, on the other hand, with a maximum torque of 194 Nm, is characterised by compact dimensions, zero backlash and a higher power density. And particularly fast switching times are also a feature, says Zysk: “The switching time of the small COMBIPERMs is just 2 ms, while the largest version has a maximum switching time of 15 ms. In this way, we help to ensure that robots can fulfil their main task: Working quickly and efficiently, saving time and costs.”
