4 new features of the F6 and S6 Drives
Hardware and software updates for KEB frequency inverters
The COMBIVERT F6 Drive Controller and the S6 Servo Drives from KEB Automation regularly receive hardware and software-based updates and new features. The requirements of customers from the plant and machine construction industry are incorporated directly into the development process. This ensures that the drive controllers continue to provide the highest level of efficient drive for various types of motors. Here is an overview of four innovations.
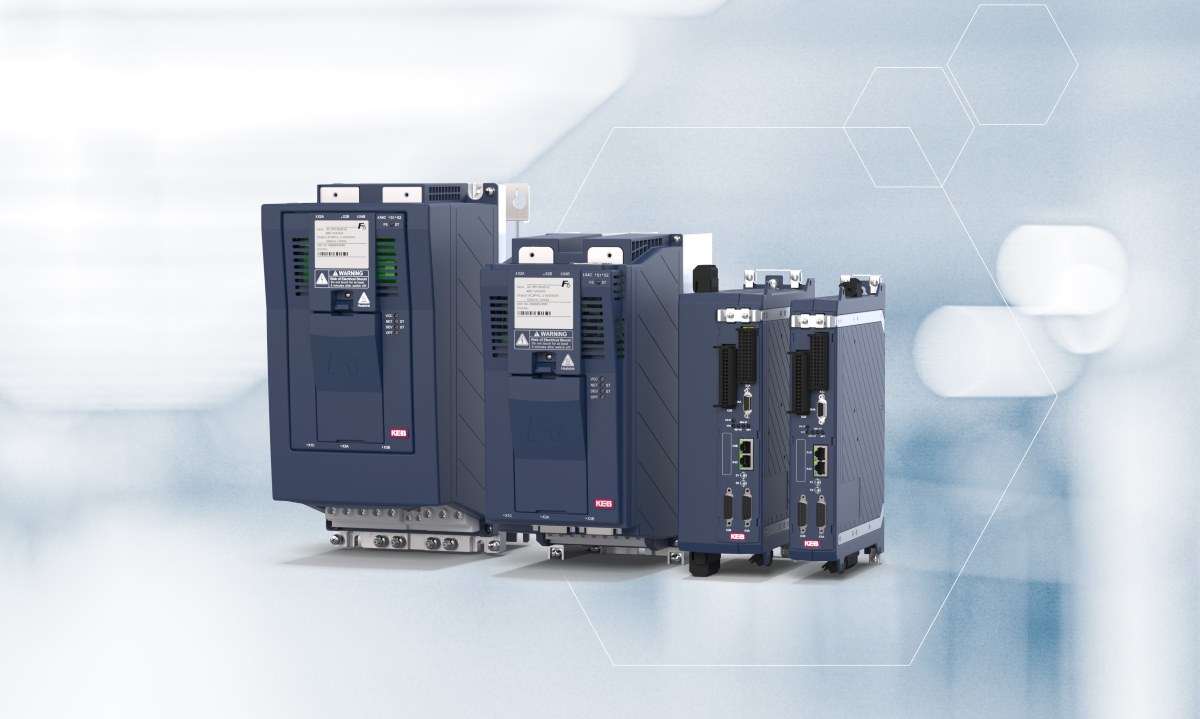
What are the latest features of the drives and what can users look forward to? A powerful high-speed version of the F6 was recently launched, with output frequencies of up to 2,000 Hz and switching frequencies of up to 16 kHz, optimised for applications such as turbo blowers, turbo compressors or spindles. The F6 portfolio has also been expanded in recent months with the Peak Power Drives. These are characterised by a higher nominal output overload and a higher software and overcurrent limit.
There are also some interesting new functionalities – and more will be available soon:
DC connectivity
“DC connections already play a major role in many systems today and their importance will continue to grow in the future in order to achieve energy savings. They make it possible to efficiently connect several inverters via a common DC link, which optimises the energy flow within the system,” says Timo Geisler, Product Manager Drives at KEB. Energy generated during braking processes is exchanged directly between the inverters. This innovation not only ensures significant energy savings, but also reduces peak loads and operating costs.
DC connections simplify cable installation and minimise the need for AC components such as chokes and filters. In addition, braking resistors can be dimensioned significantly smaller or can even be avoided altogether in some cases. The result: the complexity of the system is reduced. In addition, the extended DC connectivity improves system efficiency in systems with multiple drives and different load profiles and leads to better controllability of energy consumption and, in total, to increased overall performance of machines and systems.
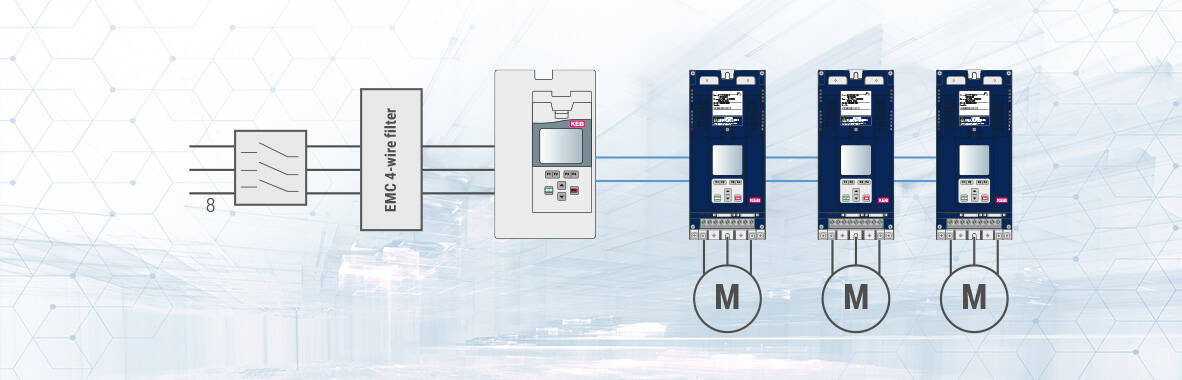
In the web seminar “Saving in the DC network”, DC connectivity is explained using the example of an injection moulding machine. Among other things, you will learn how the maximum to average feed-in power and the average braking power can be reduced by over 80 per cent.
CAN cross-communication
The new firmware for the F6 and S6 Drives enables much faster drive-to-drive communication. This includes CAN cross-communication, which is available for the APPLICATION and PRO device variants. The advantage of this is that cross-communication allows information and data to be exchanged directly between the inverters without the information having to take a “diversion” via the customer controller and other fieldbus participants. The faster data flow enables the user to achieve greater precision on the shaft and increased application performance, as torque setpoints can be adjusted on the motor, for example.
A special feature of CAN cross-communication with the KEB Drives is that users can utilise all process data-capable parameters. Whether it's torque, position or speed: plant and machine manufacturers are free to decide which data to work with.
PROFIdrive
“Our customers can look forward to another feature in the near future, as PROFIdrive will soon be available for the inverters of the Application variant,” says Tobias Wenneker, Product Manager Drives. “PROFIdrive defines the device behaviour and the access procedure to device data for electric drives on PROFINET – from simple frequency inverters to high-performance servo drives.” CiA402 has already been supported by KEB Drives for several years, which is why the introduction of PROFIdrive marks the next step. Depending on the classification of the F6 and S6 drive controllers, Speed Control Mode or Positioning Mode will then be available. Fieldbus communication via PROFINET is already possible with the Application and Pro device variants, and safe communication via PROFIsafe was introduced for the Application variant around two years ago.
COMBIVIS Dashboard
As an add-on for COMBIVIS – the software tool for the KEB Drive Controller – customers can soon expect the new dashboard. This provides a quick and easy way to get an overview of the drive controller status. Among other things, it is particularly easy to find out what type of application parameterisation is running on the drive, what firmware version is involved or what the current I/O signals are. The dashboard package will be available shortly and can be easily installed via the package installation of the COMBIVIS 6 tool.
About the COMBIVERT F6 and S6 Drive Controllers
The F6 Drive Controllers with a power range from 2.2 kW to 450 kW and the S6 Servo Drives with a power range from 0.75 kW to 7.5 kW are established in numerous applications - from intralogistics to woodworking machines. When designing the drives, the focus is always on finding the best possible drive solution for each individual case.